coaxial electrospinning Machine
Coaxial Electrospinning Machine from Spruce Science is great for producing multifunctional nanofibers.
Coaxial electrospinning is a fabrication technique where nanofibers with composite properties are produced. A second material is added in addition to the core material at the needle tip to produce fibers with multifunctional properties. Similar to the conventional electrospinning process, the coaxial electrospinning method also uses high voltage as the primary driving force to transform the polymer solution to nanoscale fibers.
The Coaxial Electrospinning Machine is configured with two syringe pumps and a coaxial spinneret that enables the delivery of two different solutions for simultaneous electrospinning. The spinneret design consists of two independent channels that combine at the tip of the needle. The second syringe pump and an extra path for solution delivery gives you a lot of flexibility to explore many novel applications.
For instance, you can electrospin coaxial fibers that has the core polymer with one particular type of material characteristics and the sheath layer that has complimentary properties. You can also use the two channels to blend together polymers. And yet another possibility is to use the second channel to delivery particles, molecules, liquids or medicine to create functional fibers.
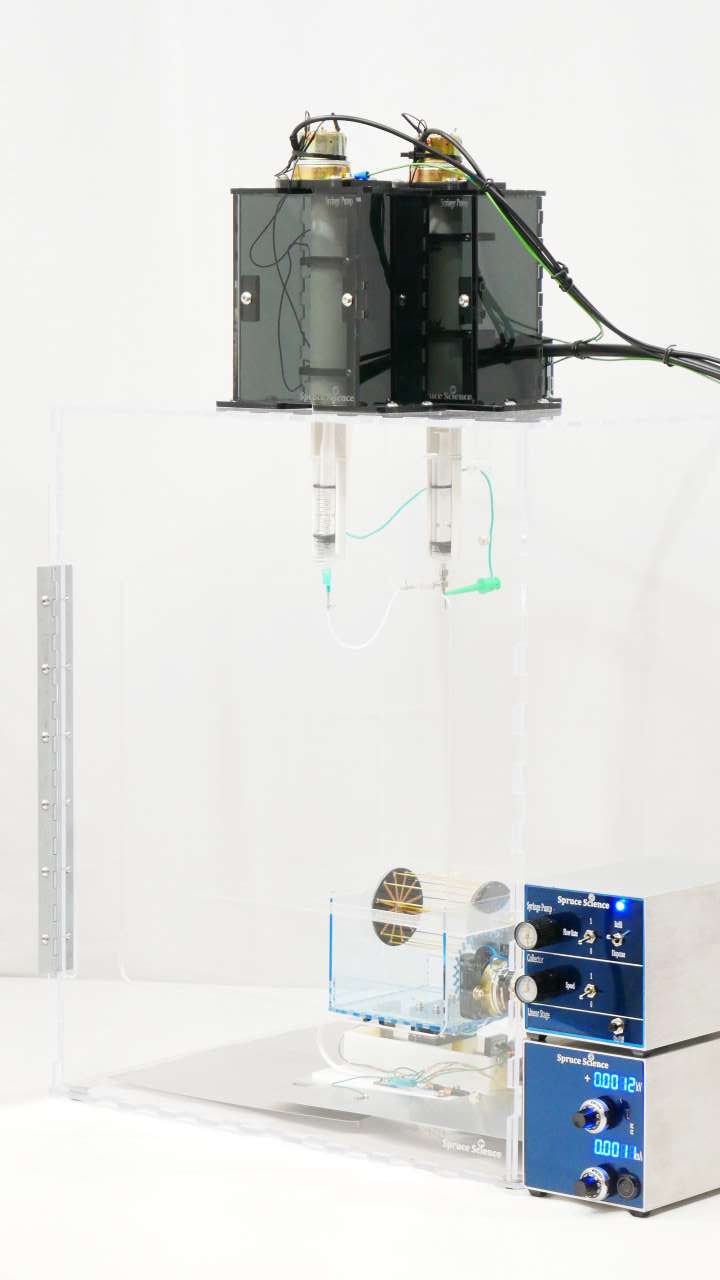
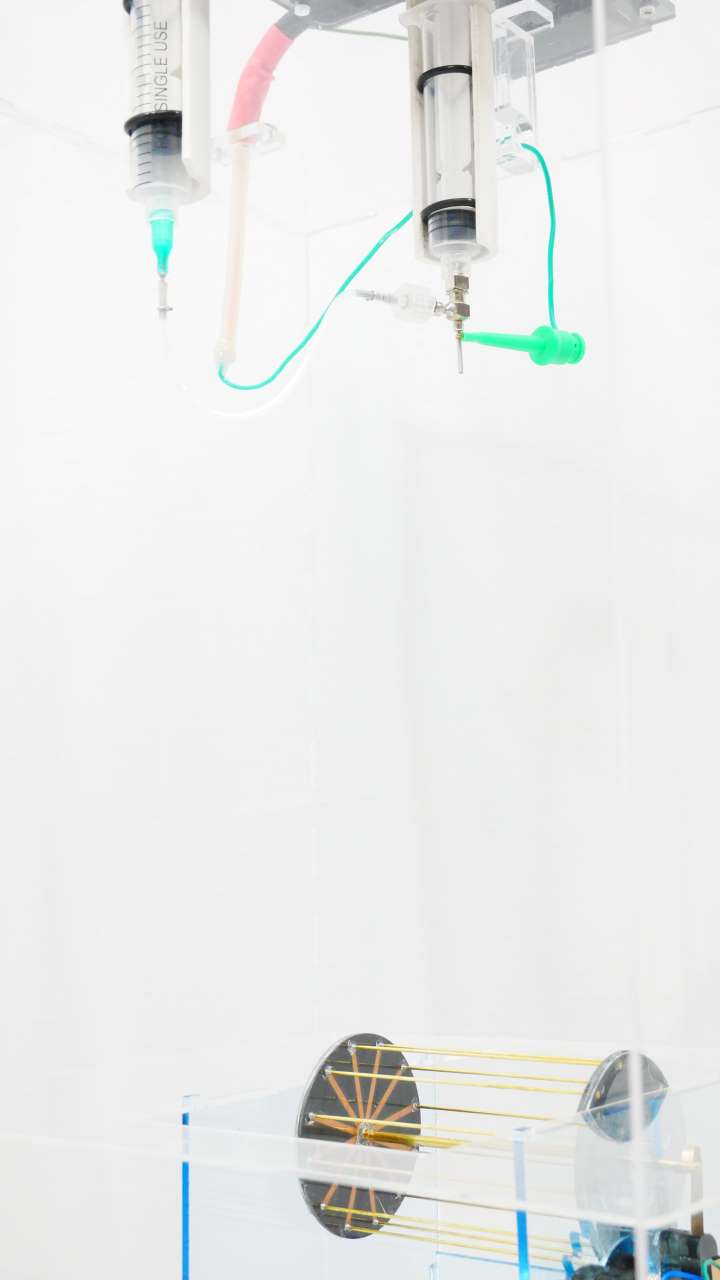
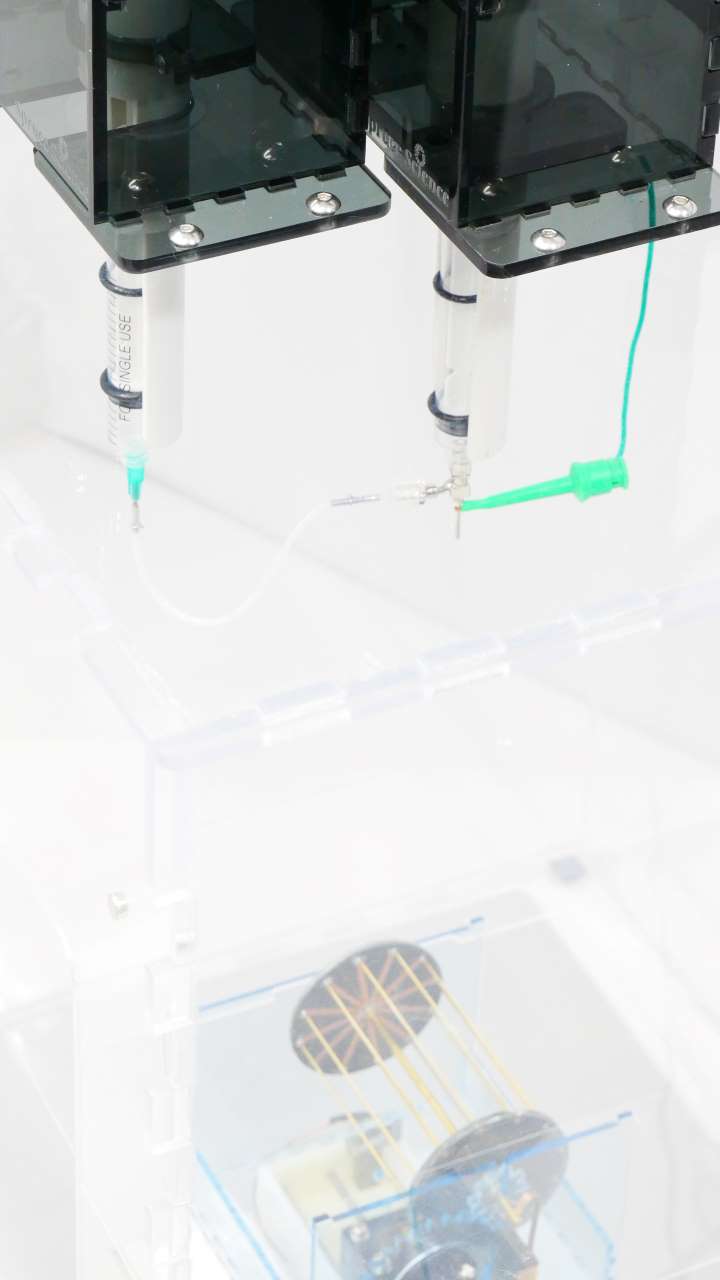
Coaxial Electrospinning Machine 30kV is fully integrated.
This fully enclosed workspace gives you more control over the electrospinning environment and is great for exploring functional nanofibers. The apparatus consists of two syringe pumps with independent flow rate control, collector module with rotation speed adjustment, and +30 kV adjustable high voltage power supply. This compact and lightweight system gives you versatility.

- Two independent syringe pumps.
- Collector with speed adjustment.
- Linear stage for the collector assembly.
- Controller for syringe pumps, collector, and linear stage.
- Benchtop high voltage power supply that is adjustable up to +30kV at 0.4mA.
Video Demonstration
Safety
Your safety is paramount and rigorous safety practices must be enforced to ensure your safety when working with high voltage.
This power supply produces high voltages and stores energy that is hazardous. Physical contact with the high voltage output may result in life-threatening or fatal injury.
Before you turn on the high voltage power supply, always confirm first that the dial indicators are turned fully in the counter-clockwise direction and confirm the turn counting indicator reads 0.
Visually inspect the high voltage output connector and any high voltage connections for unintended touching or electrical shorts.
Always keep a safe distance from the test equipment and apparatus or system under test.
Do not touch connections unless the high voltage power supply is off and capacitors are completely discharged. Allow five minutes for the high voltage power supply internal capacitors to discharge. Also, make sure the load capacitance is discharged.
Be extra cautious of any high voltage connections that are exposed. Such live terminals should be shielded and barriers must be provided to prevent accidental contact.
Proper grounding is very important. High voltage power supplies must always be grounded. Ensure that a secure ground connection is made between the high voltage power supply and earth ground.
All ungrounded terminals of the test equipment or apparatus under test should be considered as energized.
The work area for the HV power supply should be kept clean. It is important to put away unnecessary parts and components and to keep them far away from the test area.
The general work area around the HV power supply and high voltage connections must be kept dry.
Do not ground yourself or work under wet or damp conditions.
Always consult with your organization’s health and safety expert.