Electrospinning Zinc Oxide and Polyvinylpyrrolidone Composite Fibers
Electrospinning Demonstration Notes
Introduction to Nanocomposite Fibers Prepared by Electrospinning Technique
There is a lot of interest in nanocomposite fibers because of the potential applications in sensors, filtration, optoelectronics, and tissue engineering to name a few. Electrospinning is a fabrication technique that is very simple but effective method of producing nanocomposite fibers. Electrospinning process is used to produce nanofibers from many synthetic and natural polymers. A high voltage power supply is used in the electrospinning process to produce ultra small diameter fibers. Some of the attractive properties of the electrospun nanofibers are the small diameter, high porosity and high surface-to-volume ratio. Electrospun fibers have an increase in surface area and by dispersing inorganic particles, you are able to modify the properties and improve the performance. The electrospinning process is efficient since the use of materials is very minimal and production cost is low.
In the composite fiber electrospinning process, the polymer that you want to make nanofibers are mixed with a solvent and composite particles of interest are dispersed in the solution. The composite solution is loaded inside the syringe. The syringe pump flow rate is adjusted to desired flow rate and high voltage is applied to the liquid solution to create a charged jet of polymer solution. When this jet travels in air, the solvent evaporates and leaves behind a charged composite fibers. Because of the intense electric field that exists between the needle tip and rotating collector, the nanocomposite fibers are electrostatically elongated and collected on the metal sheet. The electrospinning process is simple but produces amazing results.
After reading through this electrospinning process demonstration notes, you will see Zinc Oxide (ZnO) and Polyvinylpyrrolidone (PVP) nanocomposite fibers prepared by electrospinning technique. You will see the construction of the electrospinning machine that is powered by Lab Mate high voltage power supply. You will also see the syringe pump and drum collector assembly that is compact but effective. When combined together to form the electrospinning machine, you can explore nanocomposite fibers fabrication process.
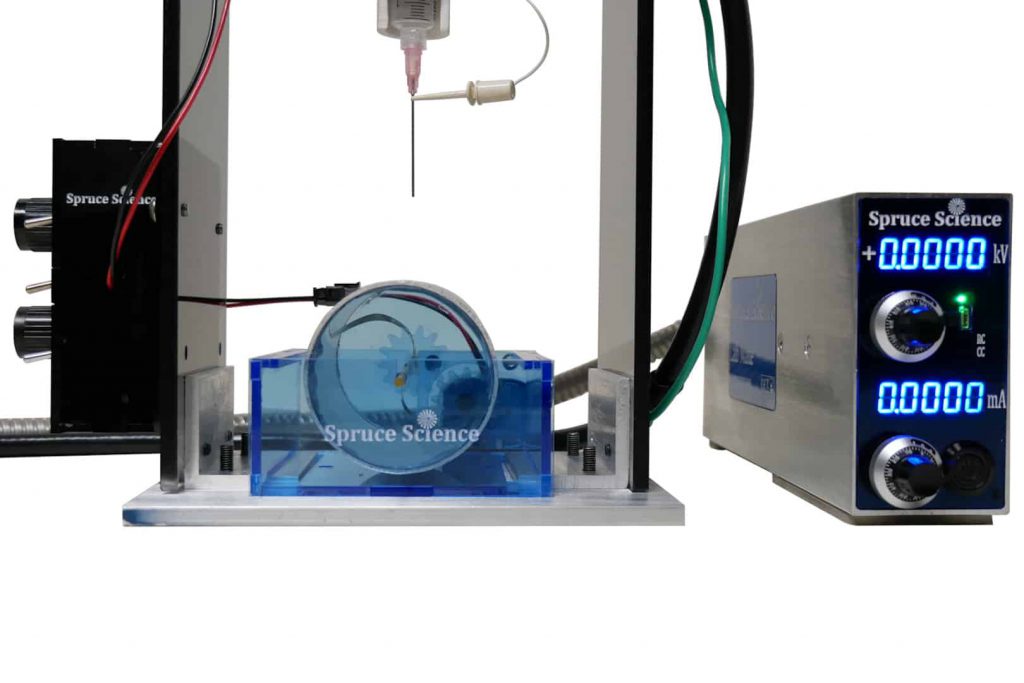
Material Overview
Polyvinylpyrrolidone (PVP) is a synthetic polymer that is amorphous and the appearance is white to light yellow. When it’s dry, PVP is a light flaky powder that is odorless and is a nontoxic material. It’s soluble in water and other polar solvents such as methanol and ethanol. The substance attracts and holds water from its surroundings. It can readily absorbs up to 40% of water by its weight. PVP solution has good wetting properties and readily forms films. It has good characteristics and is a popular electrospinning material because of the low cost and effectiveness.
Zinc oxide (ZnO) is an inorganic compound that appears white and the powder is insoluble in water. It is odorless and used as an additive in many products. Zinc oxide has high refractive index, high thermal conductivity, and good UV-protection. These properties makes it attractive for use in many applications.
The white flaky powder on the left side is PVP. On the right side is the Zinc Oxide powder.
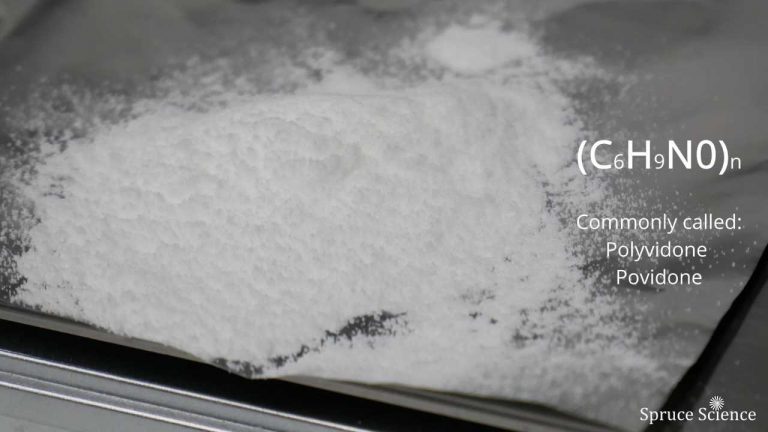
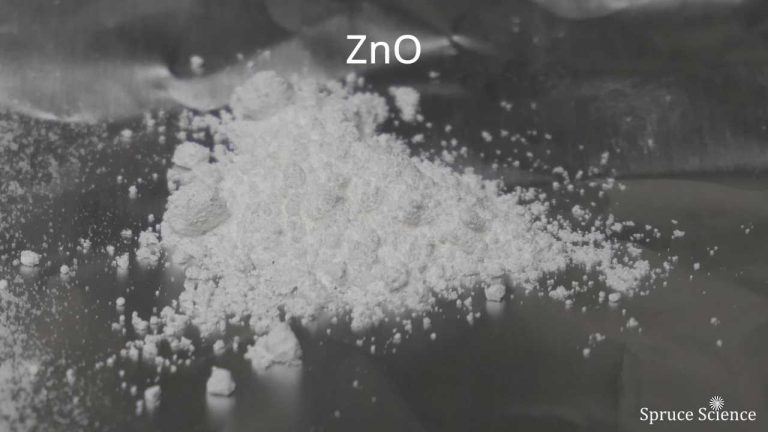
Composite Solution of ZnO Dispersed in PVP
Let us prepare the composite solution by dispersing Zinc Oxide particles in PVP solution.
We start off by weighing about 1.2 g of PVP.
Then we added 0.3 g of ZnO, which is about 25% of the weight.
Pour the powders into the plastic container for mixing.
Next, we added 70% isopropyl alcohol and mix the solution together. We first added 0.6 g of alcohol but the solution was very lumpy. So we added more alcohol and the total alcohol weight was 1.5g which is equal to the powders.
We mix everything together to form a viscous solution. This is one of the parameters that you would optimize to get the nanofibers with certain characteristics that would fit your applications or interest.
To disperse the zinc oxide powder uniformly, we are going to use an orbital sander as a mixer. For a small sample like the one we are dealing with here, we found that an orbital sander works really well. We are using a Makita orbital sander but any will do. This it is a great solution because orbital sanders are cheap and commonly available. We placed a double sided tape on the orbital sander and are using the adhesive to help secure the cup. We mix the composite solution for about a minute.
The solution forms very interesting wave patterns during the mixing process.
A side by side comparison is shown here. The clear solution on the left is the PVP solution. The cup on the right that appears white contain the ZnO particles. Adding the powder does change the characteristics. It becomes white because the ZnO particles are reflecting photons in the visible spectrum. ZnO is used in sunscreen so it also reflects UV light as well.
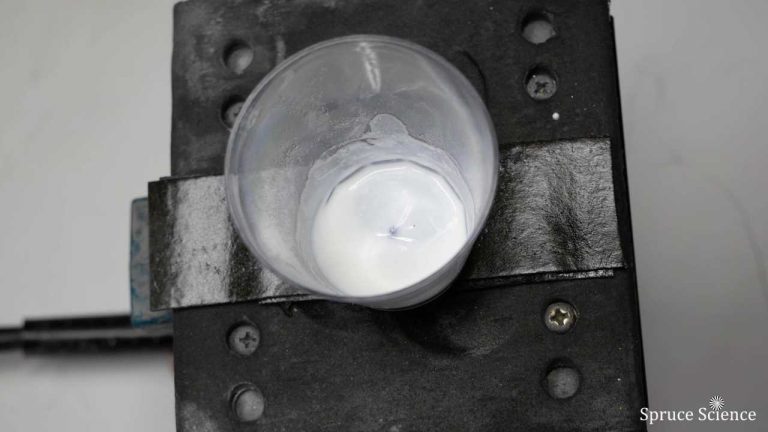
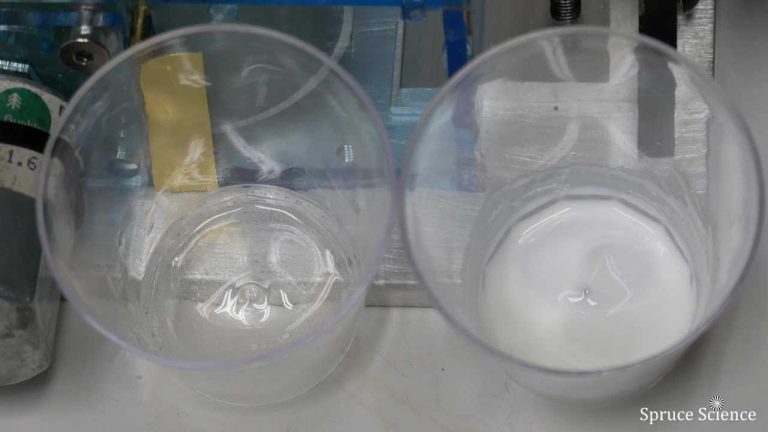
Electrospinning Machine
The apparatus used in the electrospinning process consists of the syringe pump, benchtop high voltage power supply, and collector assembly.
The syringe pump is the vessel that holds and deliver the zinc oxide plus polyvinylpyrrolidone (PVP) solution. This is the sample holder for the electrospinning process. The syringe pump is oriented in the vertical direction and a DC motor slowly pushes the polymer solution through the needle.
The primary driving force behind the electrospinning process is the intense electric field. LabMate is a benchtop high voltage power supply used in this electrospinning process to generate the intense electric field between the sample and grounded collector assembly. This particular high voltage power supply is compact and great for this type of application since the front panel provide easy control over the high voltage output. During the experiment, high voltage in the range of +15kV was applied to the liquid sample to make small fibers that are stretched electrostatically.
Electrospun composite fibers that are fabricated are then collected on the drum collector assembly. The drum collector is electrically grounded and electrically charged fibers are attracted to the drum collector. It can be rotated while the electrospun composite fibers are collected.
Each of the sub-assembly and how they function in the electrospinning process will be covered in the sections that follow. After the basics of operation is presented, the results from ZnO with PVP electrospinning will be presented. Video presentation for the electrospinning process can also be seen on the bottom of the page.
Drum Collector Sub-Assembly
The fibers that are produced in the electrospinning process are deposited on the collector assembly. This electrospinning machine utilize a drum collector that rotates and the speed is adjustable. The collector itself has an important effect on the arrangement of the nanofibers that are produced by the machine. Because of the rotation, the gathered fibers are aligned over a larger area.
The collector is electrically grounded during the electrospinning process. This is important because the potential gradient that exists steer the electrically charged fibers.
The drum collector sub-assembly can be seen below and the rotation is driven by a DC motor. The drum collector is detachable from the frame and it has spur gears attached on both sides. The drum collector material is Aluminum and the outer diameter is 2.5″.
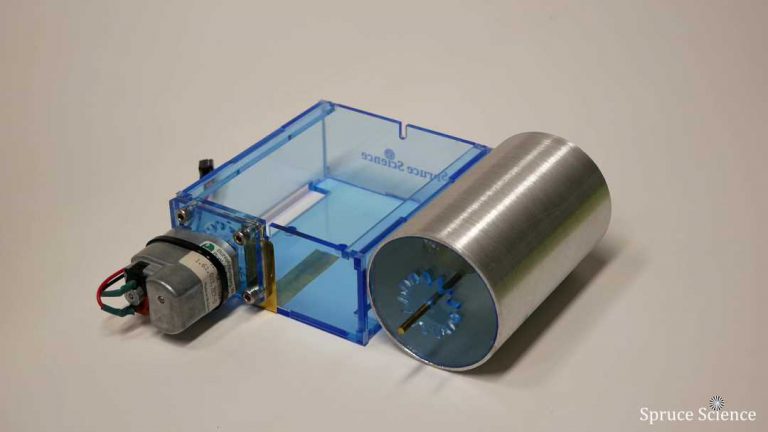
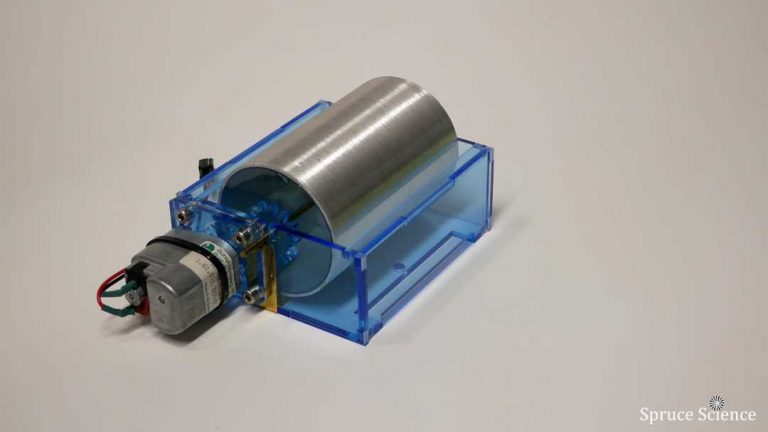
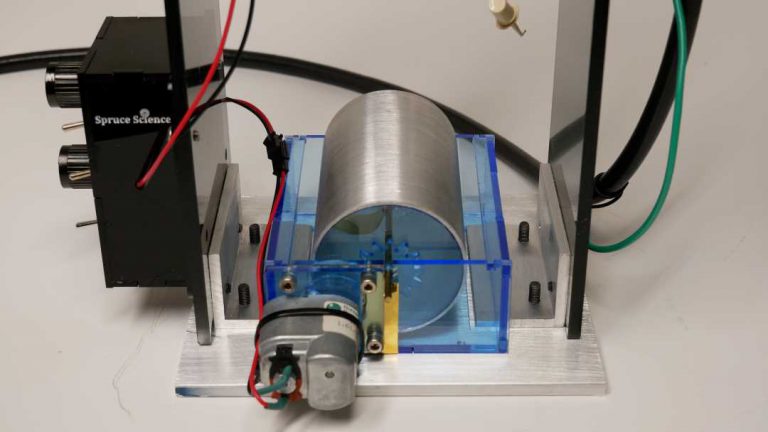
Collector preparation steps for electrospinning:
- To install the drum collector, align the gears and insert it gently in place.
- Place the collector assembly on top of the aluminum base.
- Connect the DC motor to the controller.
- Plugin 12V and provide power to the Control Panel.
- Turn-on the collector motor.
- The collector rotation speed can be adjusted by turning the dial on the Control Panel. Collector rotation speed is an important tuning parameter for the electrospinning process.
Syringe Pump Sub-Assembly
In the electrospinning process, the sample is held inside the syringe pump sub-assembly. The syringe pump is a small pump and it is used to gradually deliver a small amounts of PVP solution for electrospinning. The syringe pump is integrated into the electrospinning tower and it stands erect in the vertical direction. The syringe itself is removable from the frame and syringe driver.
The syringe pump housing is constructed from an insulating plastic tubing and this provide electrical insulation so that high voltage can be applied directly to the needle and sample solution.
The syringe pump can be seen in the pictures shown below and the following steps illustrate the syringe pump usage during the electrospinning process.
- On the Control panel, push the switch upward to “Reverse” and turn-on the Taylor Cone motor switch. The pump motor will rotate at maximum speed when traveling in the up direction.
- After the highest position is reached, carefully remove the syringe from the white tube housing.
- When you are ready to run experiments, fill the syringe with liquid sample. For alignment purposes, install two o-rings as shown. This particular syringe size is 10 cc.
- Insert the plunger end of the syringe into the white tube housing. Then lock the syringe by placing the hand tab into the slot.
- Set the pump direction to “Dispense” and turn-on the pump. When the pusher inside the white tube is engaged with the syringe plunger, liquid droplets will form at the tip of the needle.
- Dispense speed can be adjusted using the potentiometer located on the Control panel.
- Connect the HV clip to needle.
- WARNING! Make sure the high voltage power supply is OFF before touching the clip.
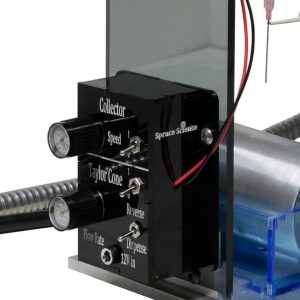
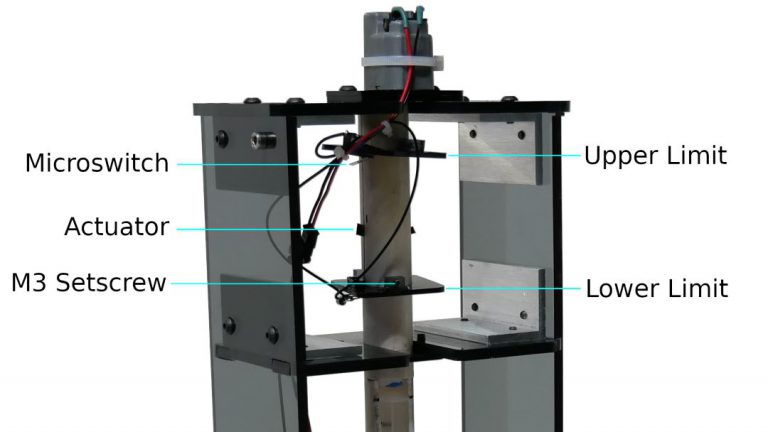
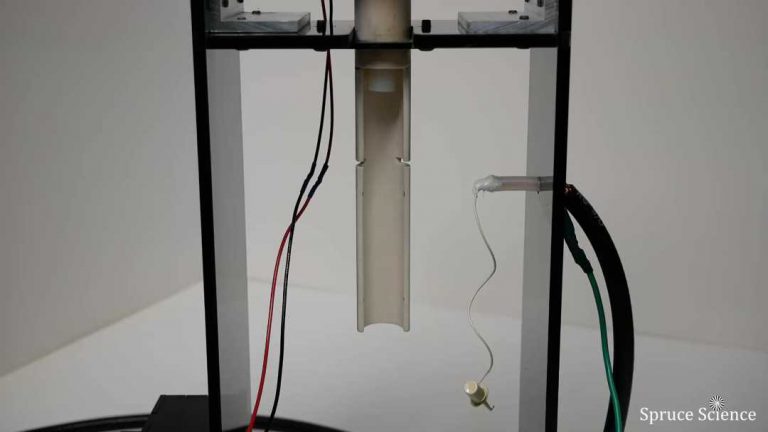
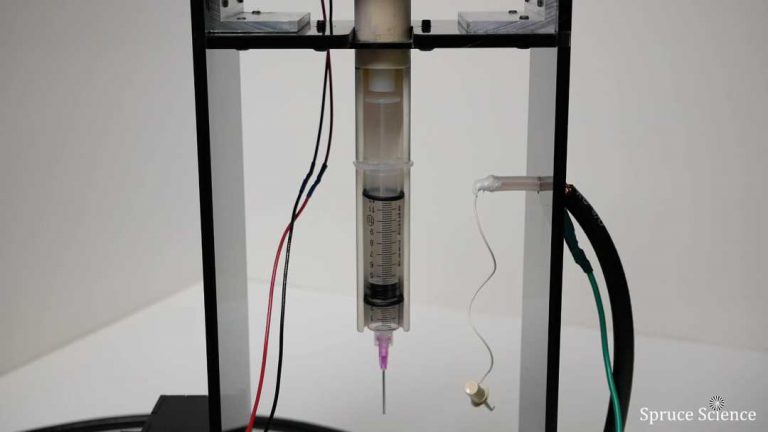
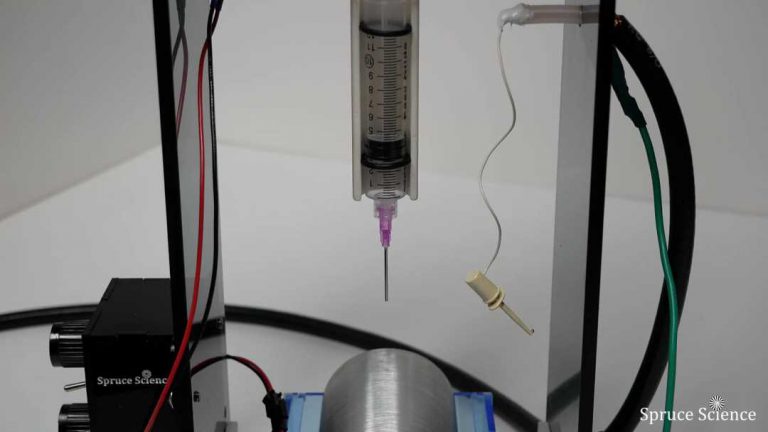
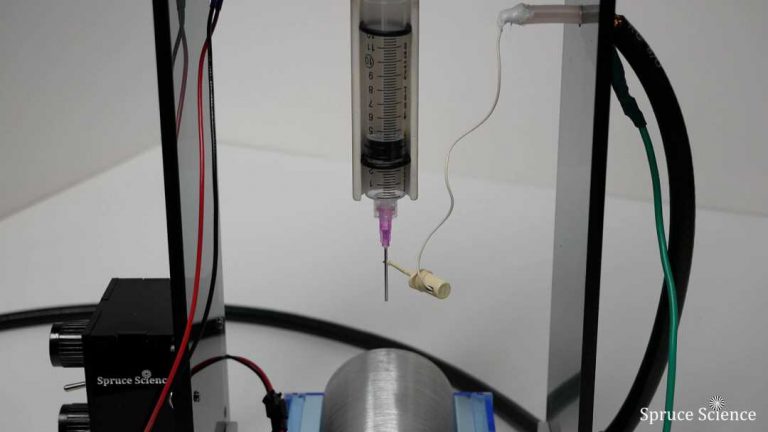
Benchtop High Voltage Power Supply
It is important to note that having a reliable high voltage power supply is absolutely critical for electrospinning since the intense electric field is the primary driving force behind the electrospinning process.
LabMate is the high voltage power supply used in this experiment and it can be seen here. LabMate is an adjustable high voltage switch mode power supply. It is compact, lightweight, and versatile. This compact high voltage power supply can produce 10kV at 2mA.
The compact form factor is great for usage in space-constrained systems since even the simplest experiments end up occupying a lot of space. It is also very convenient that the precision high voltage power supply is highly integrated because it simplifies the setup process. The only thing required from the user to get started is to plug-in.
Your front panel control for the generator are as follows: voltage displayed in 5 digits, voltage adjustment dial with turn counting indicator, remote control receptacle, indicator light when the unit is under remote control, indicator light when the unit is in constant current mode, current display, current adjustment dial, and high voltage on/off switch.
On the back of the generator, you will find M5 threaded stud for grounding, main power on/off switch, DC input connector, HV Output connector.
In order to complete the setup, high voltage connection to the Taylor Cone tower must be made. The following steps illustrate the preparation necessary to get the high voltage power supply operational for the electrospinning process.
- WARNING! It is important to note that proper grounding is very important.
- Make a secure ground connection between the high voltage power supply and earth ground.
- Make the 24V connection.
- Connect the high voltage power supply to Taylor Cone tower.
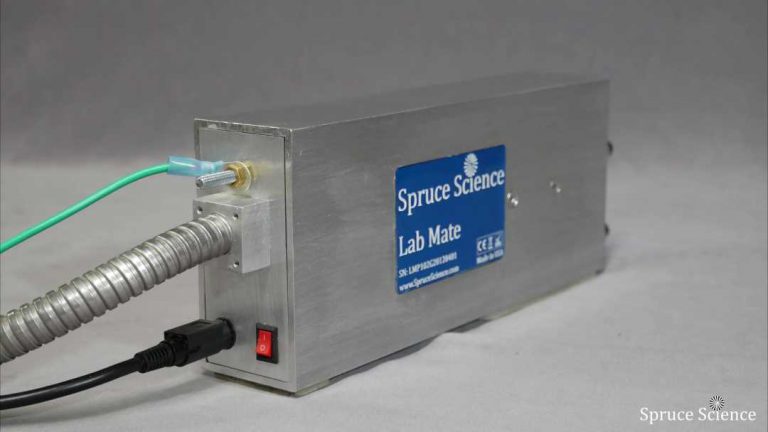
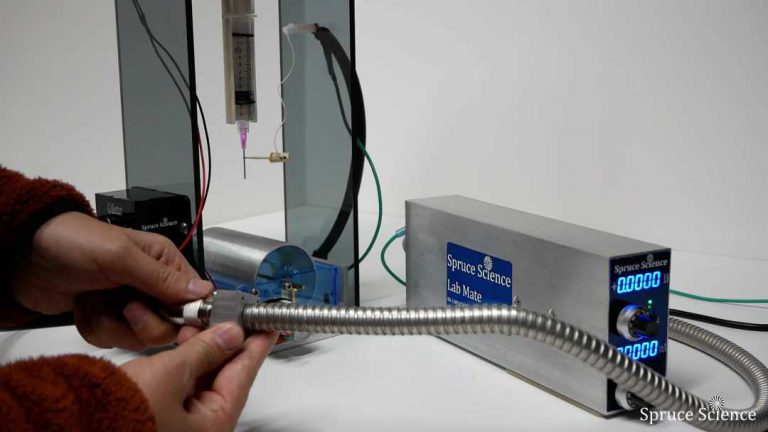
Electrospinning Process Overview
In the electrospinning process, the polymer is suspended in isopropyl alcohol inside of a syringe needle. The adjustable high voltage power supply is used to generate electrically charged fiber threads and it simultaneously establish a potential gradient between the needle tip and spinning drum collector. Under the intense electric field, these nano fibers are electrostatically elongated and collected.
1. To start the electrospinning process, begin by preparing the sample. In this demonstration, zinc oxide and polyvinylpyrrolidone (PVP) composite solution is used for electrospinning. It is mixed together with alcohol then the mixture is loaded into the 10cc syringe. The syringe pump is then used to slowly deliver the PVP solution to the tip of the needle at a constant rate so that high voltage can be applied for electrospinning fibers.
2. Depositing the electrospun fibers on an aluminum foil works well because it is easier to gather samples with different parameters that you can go back to analyze later. This will help you fine tune the parameters for the electrospinning process.
3. We are using double sided tape to hold the aluminum foil in place. Wrap the foil around the drum collector and try to keep it tight and cut off the excess foil.
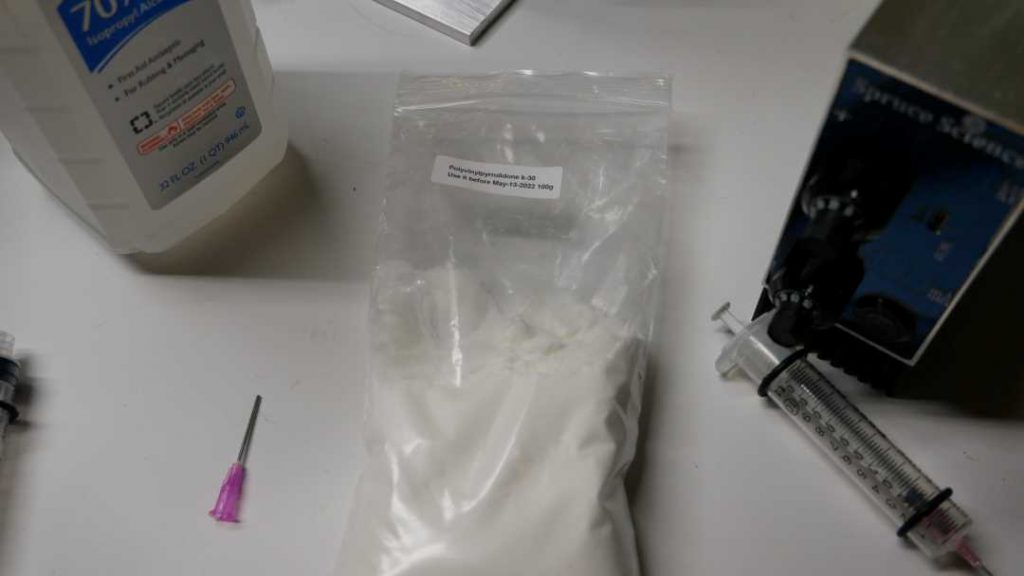
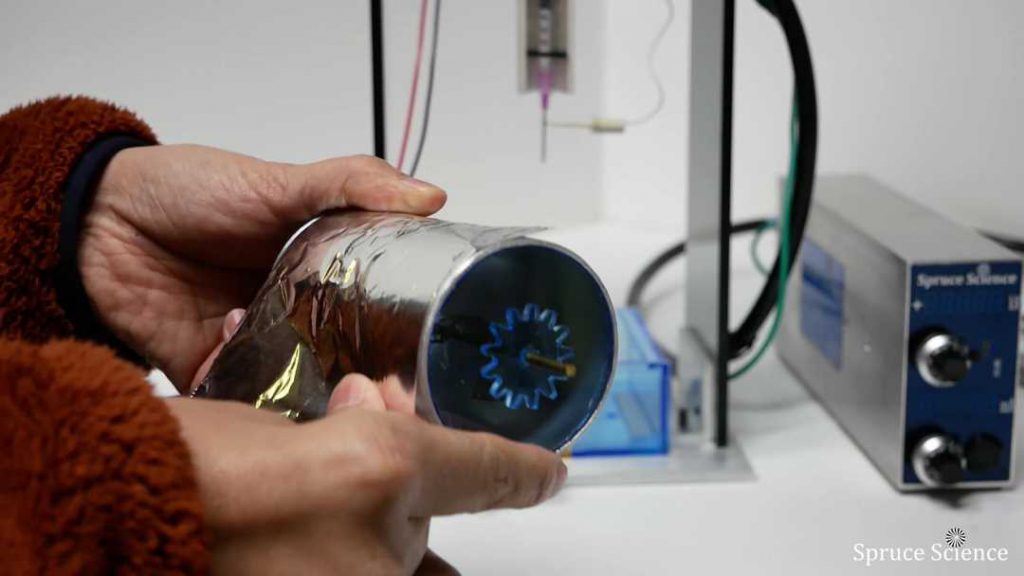
4. After the metal foil wrapping is complete, put the drum collector back in place.
5. From the control panel, set the syringe pump flow rate and collector speed. After that, turn on the motors.
6. On the high voltage power supply, adjust the current setting to the smallest output value that will work for your setup. In this particular demonstration, electorspinning did not require any current output so the current limit was kept below 0.1 mA. This will limit the current output in case there’s a short.
7. Next, set the high voltage using the dial indicator.
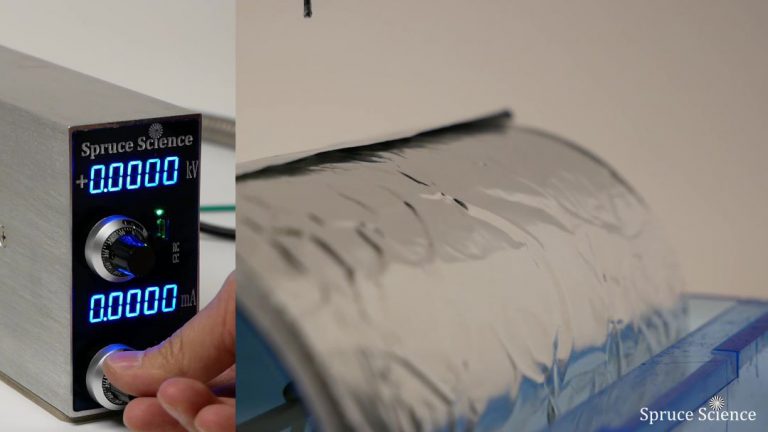
8. When everything is in place, turn-on the high voltage output.
9. Observe the electrospinning action and adjust the high voltage value, collector speed and pump flow rate to get the desired result. Tuning parameters is an important part of the electrospinning process.
Here are some parameters for you to consider when tuning the electrospinning process:
- Characteristics of the polymer such as structure and molecular weight
- Properties of the composite solution such as viscosity, surface tension, solvent type, dielectric constant and conductivity.
- Nanoparticle properties and how well it disperse in solutions. As well as type, size, morphology, concentration and surface charge of the particles.
- Process parameters such as the electric potential and charge carried by the electrospinning jet, sample flow rate, and collector motion.
- Fabrication conditions such as temperature, humidity and air velocity
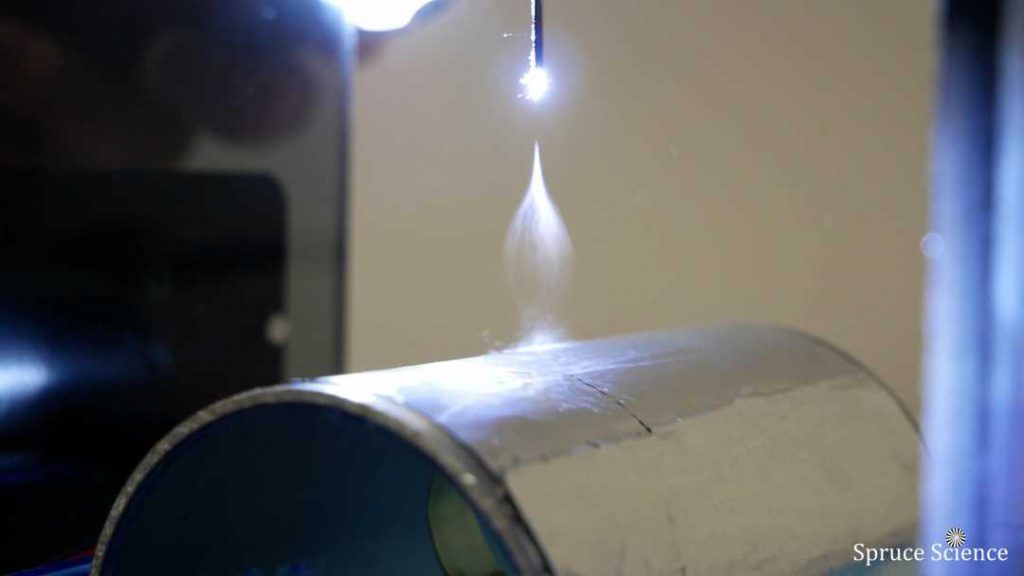
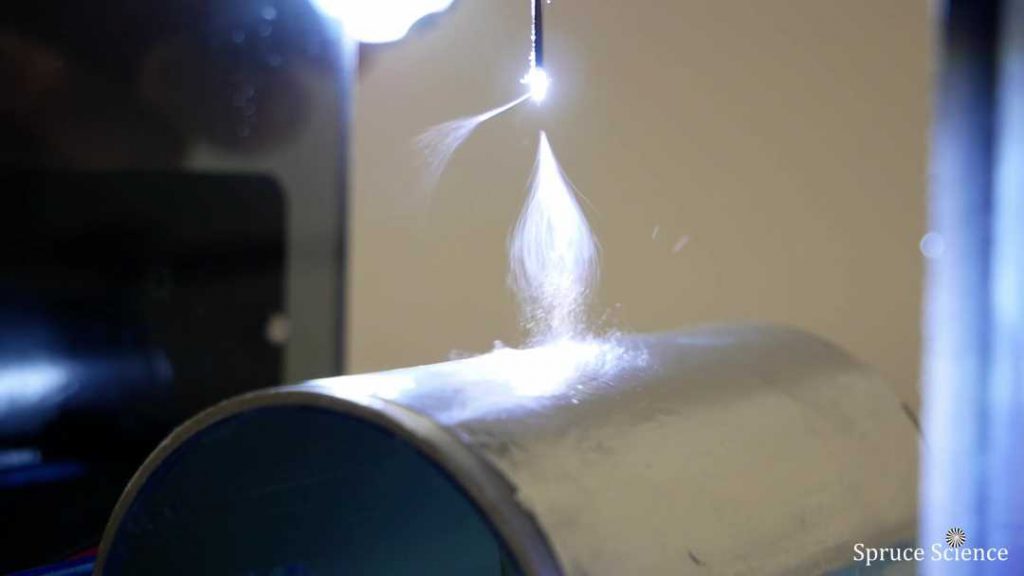
Electrospun Fibers
The electrospun fibers near the drum collector are the composite of PVP with zinc oxide fibers. This technique is pretty amazing! And they look like spider webs.
The applied voltage here is positive 15.4 kV. The sign of the voltage drop across the liquid sample to the ground plate will determine which ion types we are looking at. In this demonstration, positive high voltage output is connected to the needle and the ground collector is negatively charged, meaning that positively charged ions are selected in the electrospinning process.
When high voltage is applied from the needle, which is carrying a liquid flow, to the ground plate, there is this characteristic formation known as a Taylor cone. That Taylor cone is then pulled into a jet. From there, the jet is further disrupted into tiny fibers. This characteristic formation is established when high voltage is balanced with pumping rate.
The general observation for the electrospinning process is that if the applied voltage is too high and extraction field exceeds pumping rate, there are multiple spraying jets. However, if the applied electric field is too low, it leads to instability. For performance tuning, having an adjustable high voltage power supply is essential.
Here are some microscope images of the composite fibers of PVP with Zinc Oxide. In some cases, the fibers fused together after they dried on the collector surface.
The dispersion of Zinc oxide particles into PVP fibers can improve thermal stability and provide UV protection since it reduces UV and Visible light transmission. In addition, it can also enhance morphological and optical properties.
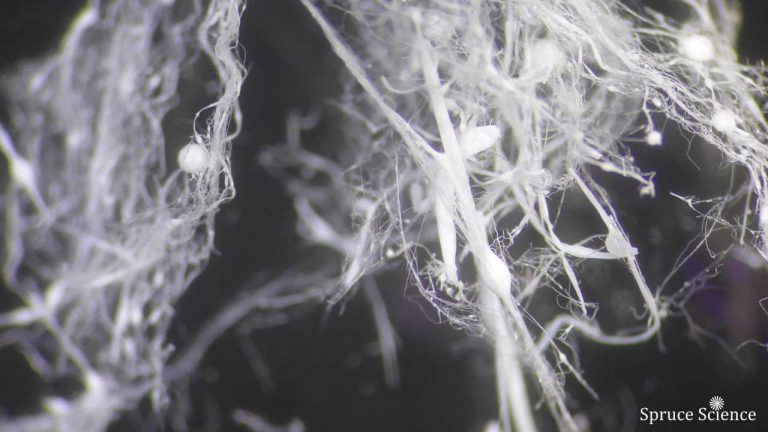
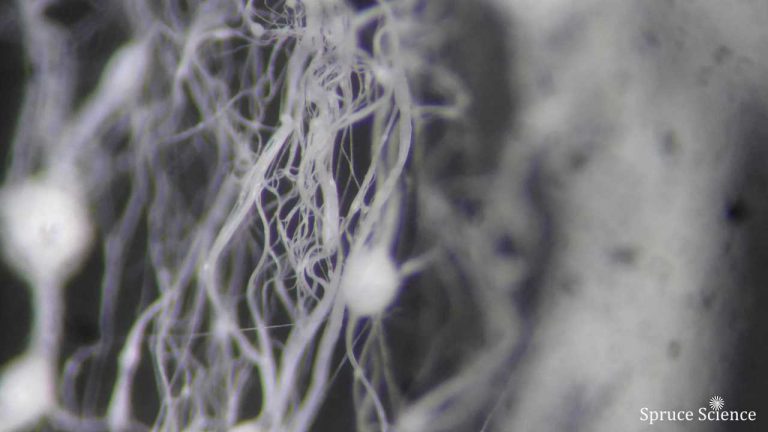
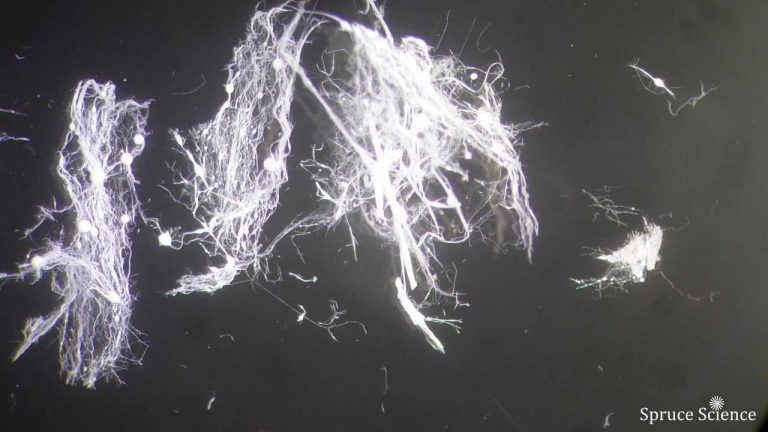
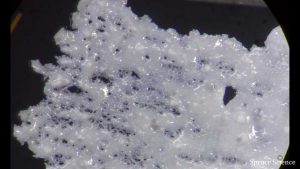
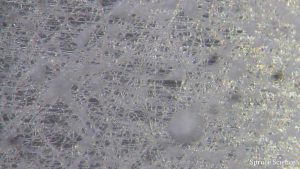
Summary
Electrospinning machine is the special equipment that you use to produce and collect the nano-scale composite fibers.
Electrospinning is performed using a syringe pump, a collector and an adjustable high voltage power supply.
Electrospun fibers have an increase in surface area and by dispersing inorganic particles, you are able to modify the properties and improve the performance. This open up the opportunity for researchers to look for new applications.
In general, primary parameters that affect the final structure of the electrospun nanofibers are the sample viscosity, dielectric constant, surface tension of the solution, solution feed rate, and high voltage applied to the polymer solution between the syringe needle and collector. The interplay of these parameters determine the constituting fiber diameter and morphology.
Electrospinning of composite fibers is very interesting. There is a lot of research interest in nanocomposite fibers because you can enhance performance and characteristics.
Electrospinning is a fascinating fabrication technique. With a small benchtop setup like the one you’ve seen, you can do a lot of interesting research and development.
Electrospinning Process Video Demonstration
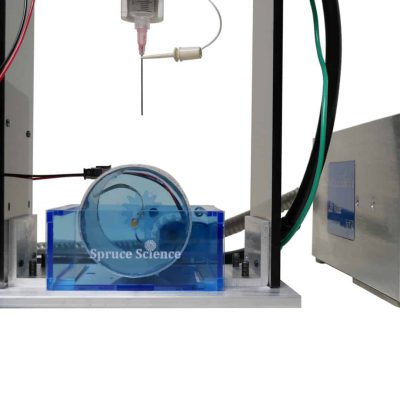